The field of robotics is undergoing a period of rapid and transformative evolution, driven by advancements in artificial intelligence (AI), sensor technology, materials science, and human-machine interaction. In 2024 and looking ahead to 2025, several key trends are emerging that promise to reshape industries, redefine human-robot collaboration, and expand the capabilities of robotic systems in unprecedented ways. These trends are not isolated but rather interconnected, building upon each other to create a future where robots are more intelligent, adaptable, and integrated into our daily lives and workplaces.
- The Ascendancy of Artificial Intelligence in Robotics:
The integration of AI, particularly machine learning (ML) and generative AI, is arguably the most significant driving force behind the current wave of robotic innovation. AI is moving beyond simply enabling robots to perform pre-programmed tasks to empowering them with the ability to perceive, learn, reason, and adapt to complex and dynamic environments.
AI-Driven Autonomy and Decision-Making: Robots are becoming increasingly autonomous, capable of making decisions and executing tasks with minimal human intervention. This is fueled by advancements in computer vision, natural language processing (NLP), and sophisticated algorithms that allow robots to understand their surroundings, interpret instructions in natural language, and plan their actions accordingly. For instance, AI-powered autonomous mobile robots (AMRs) in warehouses can navigate complex layouts, identify and pick items, and adapt to changes in inventory and workflows in real-time.
Generative AI for Robot Programming and Interaction: The emergence of generative AI models, popularized by tools like ChatGPT, is revolutionizing how robots are programmed and how humans interact with them. Robot manufacturers are developing AI-driven interfaces that allow users to program robots intuitively using natural language instead of complex code. This lowers the barrier to entry for robot deployment and enables workers without specialized programming skills to set up and adjust robot tasks. Similarly, generative AI is enhancing human-robot interaction through more natural and conversational interfaces.
Physical AI and Simulation: A significant trend is the development of “Physical AI,” where robots are trained in virtual environments that simulate real-world physics and conditions. This allows robots to learn through experience in a safe and cost-effective manner before being deployed in physical environments. Robot and chip manufacturers are investing in dedicated hardware and software to create these realistic simulation platforms, aiming for a “ChatGPT moment” for physical AI that will dramatically accelerate robot learning and adaptation.
Predictive Maintenance and Optimization: AI and ML algorithms are being used to analyze vast amounts of data generated by robots during operation. This enables predictive maintenance, identifying potential equipment failures before they occur, thus minimizing downtime and saving significant costs, particularly in industries like automotive manufacturing. Furthermore, analyzing data from multiple robots performing the same process allows for optimization of workflows and identification of best practices.
- The Expanding Capabilities of Collaborative Robots (Cobots):
Human-robot collaboration remains a dominant trend, with cobots evolving to take on a wider range of applications and work more seamlessly and safely alongside human workers.
Enhanced Safety Features: Advances in sensors, vision systems, and smart grippers are enabling cobots to perceive their environment in real-time and react dynamically to the presence of humans. This includes features like force limiting, collision detection, and emergency stops that ensure safe interaction without the need for traditional safety cages.
New Applications and Industries: Cobots are no longer limited to simple pick-and-place tasks in manufacturing. Their applications are expanding rapidly into areas like welding, painting, quality inspection, assembly of delicate electronics, food handling, and even healthcare for tasks like patient assistance and rehabilitation. The shortage of skilled workers in areas like welding is a significant driver for the adoption of cobot welding applications.
Mobile Cobots (Mobile Manipulators): Combining the dexterity of cobot arms with the mobility of autonomous mobile robots (AMRs) is creating a new class of “mobile manipulators” or “MoMas.” These robots can navigate complex environments and perform manipulation tasks in various locations, making them ideal for material handling in logistics, automotive, and aerospace industries, as well as for inspection and maintenance tasks on machinery and equipment.
User-Friendly Programming and Interfaces: Cobots are becoming easier to program and operate, thanks to intuitive interfaces, drag-and-drop programming, and the aforementioned natural language programming enabled by generative AI. This ease of use makes them accessible to a wider range of businesses, including small and medium-sized enterprises (SMEs).
- The Rise of Humanoid Robots:
Humanoid robots, designed to resemble and move like humans, are gaining significant traction, moving beyond research labs into practical applications.
General-Purpose vs. Task-Specific Humanoids: While the vision of general-purpose humanoids capable of performing a wide variety of human tasks is still some way off, significant progress is being made. Start-ups are actively developing such robots. However, industrial manufacturers are also focusing on developing humanoid robots for specific, single-purpose tasks, particularly in sectors like automotive and warehousing, where their human-like form factor allows them to integrate more easily into existing infrastructure and workflows designed for humans.
Dexterity and Manipulation: A key area of advancement is in improving the dexterity and manipulation capabilities of humanoid robots. Breakthroughs in hand design, sensor integration, and AI-powered control systems are enabling them to perform more complex and delicate tasks, such as picking and placing small objects, using tools, and even performing assembly operations. The development of advanced dexterity is crucial for the widespread adoption of humanoids in industry and society.
Mobility and Navigation: Enhancing the mobility and navigation skills of humanoids is another critical focus. This includes improving their balance, gait, and ability to navigate uneven terrain and cluttered environments. Advancements in bipedal locomotion and AI-driven navigation are making humanoids more versatile and adaptable.
Potential Applications: Humanoid robots hold immense potential in various sectors, including logistics and warehousing (handling and moving goods), healthcare (assisting patients, providing care), hospitality (customer service), construction (performing manual tasks), and even domestic environments in the long term.
- The Growing Importance of Digital Twins:
Digital twin technology, which involves creating a virtual replica of a physical system (including robots and entire factories), is becoming increasingly crucial for optimizing robot performance, reducing costs, and improving efficiency.
Simulation and Testing: Digital twins allow for the simulation and testing of robot programs and deployments in a virtual environment before they are implemented in the real world. This helps identify potential issues, optimize robot movements, and reduce the risk of errors or collisions, saving time and resources.
Real-Time Monitoring and Analysis: By connecting to the real-world robot through sensors and data streams, the digital twin provides a real-time view of the robot’s performance, health, and operational status. This enables continuous monitoring, early detection of anomalies, and proactive maintenance scheduling.
Optimization and Improvement: Digital twins can be used to analyze historical and real-time data to identify areas for improvement in robot performance, such as cycle times, energy consumption, and accuracy. They can also be used to test and validate the impact of software updates or changes to robot configurations before they are deployed.
Virtual Training and Operation: Digital twins, combined with virtual reality (VR) and augmented reality (AR), are transforming robot training and operation. They provide immersive and safe environments for training robot operators and technicians, allowing them to practice complex tasks and procedures without the risk of damaging equipment or causing injury. Remote operation of robots through digital twins is also becoming increasingly feasible, particularly in hazardous environments.
- Sustainability and Energy Efficiency in Robotics:
With growing global concerns about environmental sustainability, there is an increasing focus on making robots and robotic systems more energy-efficient and environmentally friendly.
Lightweight Materials and Design: Efforts are underway to develop robots with lightweight materials and optimized designs to reduce their energy consumption during operation. This includes using advanced composites and optimizing the mechanics of robot movement.
Energy-Saving Modes and Power Management: Implementing different levels of sleep modes and intelligent power management systems in robots can significantly reduce their energy consumption when they are not actively performing tasks.
Sustainable Manufacturing and Disposal: There is a growing awareness of the environmental impact of robot manufacturing and disposal. Research is focusing on developing more sustainable manufacturing processes and designing robots for easier disassembly and recycling.
Robots for Green Energy and Sustainability: Robots are playing a crucial role in the production of green energy technologies, such as solar panels and batteries for electric vehicles. Their precision and efficiency are essential for cost-effective and sustainable manufacturing of these products. Robots are also being deployed in recycling and waste management to improve efficiency and reduce environmental impact.
- Expanding Applications Across Diverse Industries:
Robotics is no longer confined to traditional manufacturing and logistics. Its applications are expanding rapidly into a wide range of new industries.
Healthcare Robotics: Beyond surgical robots, robots are being developed for patient care (assistance with daily tasks, companionship), rehabilitation (exoskeletons), diagnostics (AI-powered image analysis), and hospital logistics (drug delivery, automated dispensing). Soft robotics is particularly promising for handling delicate biological tissues and interacting safely with patients.
Agriculture Robotics: Agricultural robots are being used for tasks like planting, harvesting, weeding, crop monitoring, and livestock management, addressing labor shortages and improving efficiency and sustainability in farming.
Construction Robotics: Robots are entering the construction industry for tasks such as bricklaying, welding, painting, demolition, and even 3D printing of entire buildings, improving safety, speed, and precision.
Hospitality and Service Robotics: Robots are being deployed in hotels, restaurants, and retail for tasks like cleaning, food preparation and delivery, shelf stocking, and customer service. While challenges remain in replicating human interaction, advancements in AI and HRI are making progress.
Exploration and Hazardous Environments: Robots are essential for exploring space, deep sea environments, and handling hazardous materials, performing tasks that are too dangerous or inaccessible for humans.
Education and Research: Robots are increasingly used as educational tools to teach STEM concepts and as research platforms for advancing AI, control systems, and human-robot interaction.
- Advancements in Human-Robot Interaction (HRI):
As robots become more integrated into human environments, the field of HRI is becoming increasingly important. The goal is to create robots that can interact with humans in a natural, intuitive, and safe way.
Natural Language Communication: Enabling robots to understand and respond to natural language commands and questions is a key area of research. Advancements in NLP and voice recognition are making robots more conversational and easier to interact with.
Gesture Recognition and Non-Verbal Communication: Robots are being equipped with sensors and AI algorithms to interpret human gestures, facial expressions, and other non-verbal cues, allowing for more nuanced and intuitive interaction.
Socially Assistive Robots: Robots designed to provide social support, companionship, and motivation are emerging in areas like elder care, therapy, and education. These robots require advanced HRI capabilities to build trust and rapport with users.
Personalized Interaction: Future robots will likely be able to learn individual user preferences and adapt their behavior and communication style accordingly, leading to more personalized and effective interactions.
Safety and Trust: Ensuring the physical and psychological safety of humans interacting with robots is paramount. Research in HRI focuses on designing robots that are not only physically safe but also predictable and trustworthy in their behavior.
Conclusion:
The robotics landscape in 2024 and 2025 is characterized by a powerful convergence of technological advancements, particularly in AI, and an expanding recognition of the transformative potential of robots across diverse industries. The trends discussed above – the rise of AI-driven autonomy, the expanding capabilities of cobots, the progress in humanoid robotics, the increasing importance of digital twins, the focus on sustainability, the broadening range of applications, and the advancements in human-robot interaction – are shaping a future where robots are more intelligent, collaborative, adaptable, and integrated into the fabric of our lives and work. While challenges remain in areas like cost, scalability, and ethical considerations, the momentum behind these cutting-edge trends suggests a profound and accelerating impact of robotics on society in the years to come. The continued innovation in these areas will not only enhance productivity and efficiency but also create new opportunities and redefine the relationship between humans and machines.
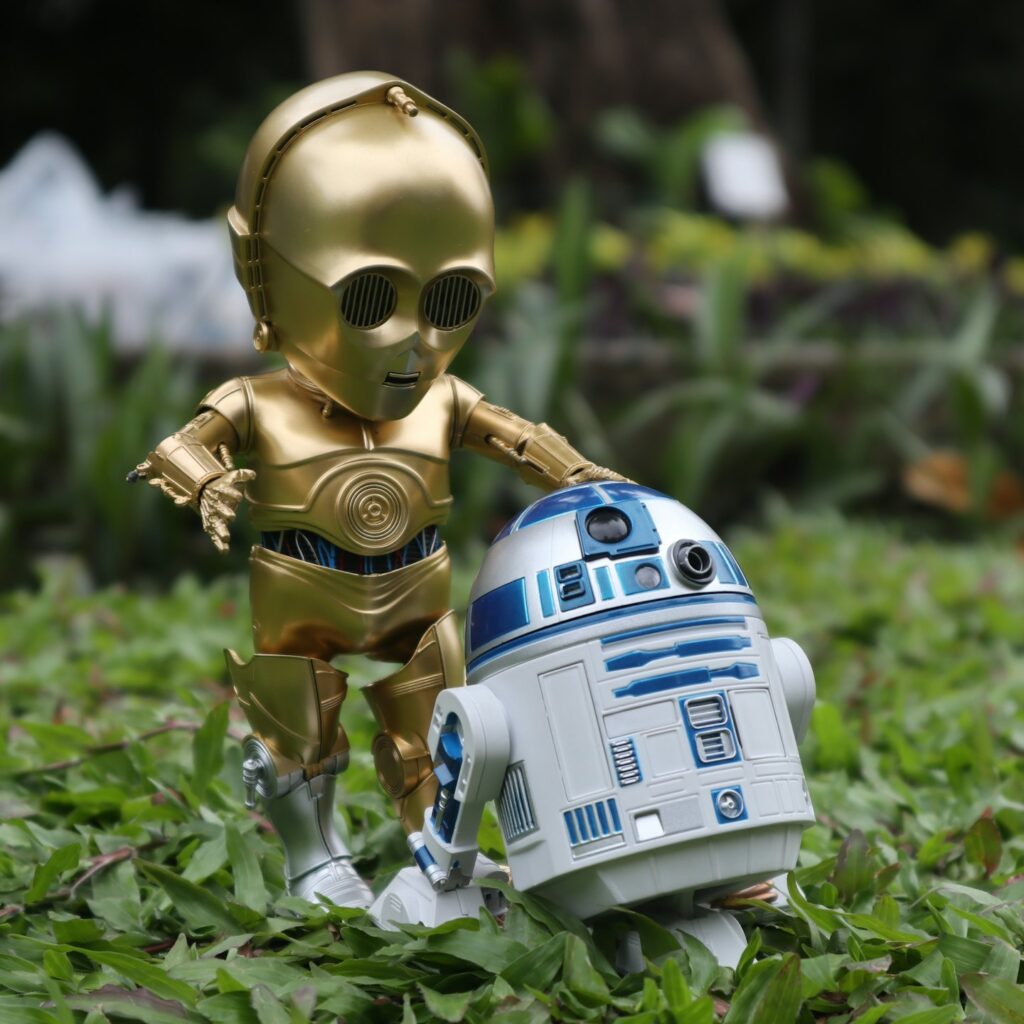
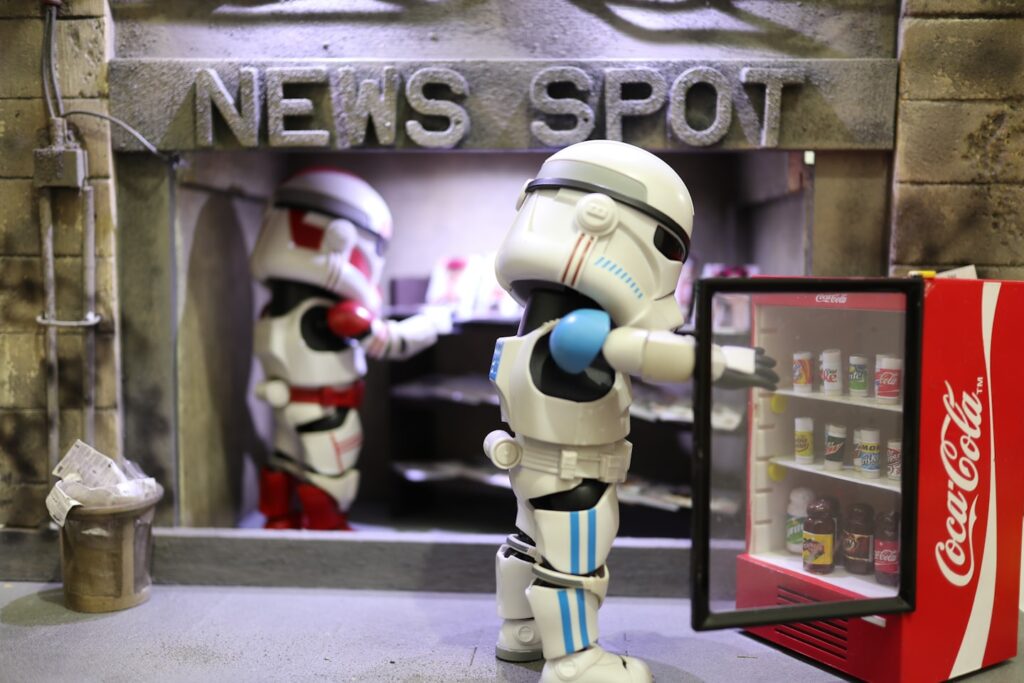